It’s Like Disneyland for Geeks
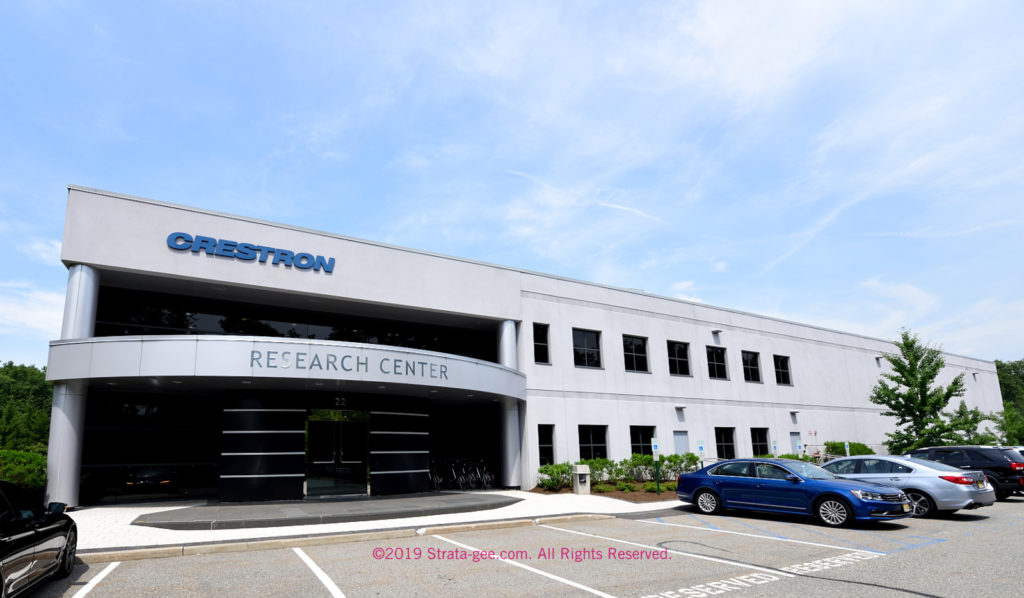
Sometimes, I’m amazed at what I’m able to pull off. A year or so ago, John Clancy, Crestron Vice President of Residential, invited me to tour Crestron, a place I’ve heard much about but have never seen. OK…it was at a tradeshow cocktail party and John may have been drinking…but I immediately jumped at the opportunity. Just a few weeks ago, that visit finally happened and Crestron – much to their credit – granted me unlimited access to whatever I wanted to see…and photograph.
Go inside the amazing Crestron Research Center with Strata-gee…
I feel uniquely qualified to be your tour guide on this adventure. As some Strata-gee readers know, I was once a top executive at an audio manufacturing company who toured many factories around the world (not to mention many engineering labs). I find these inner workings of companies to be extremely fascinating – and revealing. You can get a real sense of the amount of true power behind a brand…or lack thereof…by going behind the scenes.
In my tour of Crestron, I visited three separate facilities – the Research Center, the all-new Orangeburg “Factory of the Future” (more on this later), and their main headquarters building with extensive education and training center, which also houses a full showroom/experience center.
It was a long day and I took somewhere between 400-500 photographs of these very impressive facilities. I will break down my reporting on this visit into three separate posts over as many weeks.
So for this post #1 of 3, we will start this week with the amazing Crestron Research Center…
FULL DISCLOSURE – In order to have unlimited photographic access, I had to agree to allow Crestron management to review my photos of the Research Center prior to publication. The purpose of this was to prevent any accidental exposure of future products before they’ve been announced.
Although I normally decline such agreements, in order to speed our day along, I made an exception in this case and agreed, based on a gentleman’s understanding that no image would be unreasonably withheld. As part of this agreement, Crestron management received access to a private gallery of photos from the Research Center that they could view and then submit a request for the specific images they felt needed to be pulled.
Fortunately, and again to their credit, Crestron management made no such photo removal requests. They did, however, have one concern. I will reveal what that concern was a little later in this post.
>>Click to see a slide show of all of my photos from Crestron’s Research Center<<
You’ll See What I Saw
Since Crestron’s management did not request I remove any photos, between here and a slide show I’ll share with you from my content distribution network, you will find almost all of the photos I took. You will see with your own eyes exactly what I saw with mine.
It was a typical sunny day in July that was quite warm and humid – thunderstorms and rain were predicted and we would experience both of them before the visit concluded. Thanks to New York Metro area traffic, I arrived about 20 minutes late to Crestron’s Northern New Jersey campus that houses four large buildings – with other buildings off-campus in the surrounding area.
For those of you unfamiliar, this is a really pretty part of the state, lush green vegetation, with many fields, trees, and woods throughout the area. In fact, I was surprised at how rural the area seemed to be, with small, two-lane almost country roads winding throughout the area over hill and dale.
Greenery & Car Horns
If you look closely at the image of the Crestron Research Center at the beginning of this post, you’ll see plenty of trees and greenery off to the right and left of the building. Although we were in a large corporate park that was once dominated by Volvo (who are still there, but with a more modest presence), it feels quite rural – with no typical New Jersey traffic sounds of loud trucks or car horns blaring.
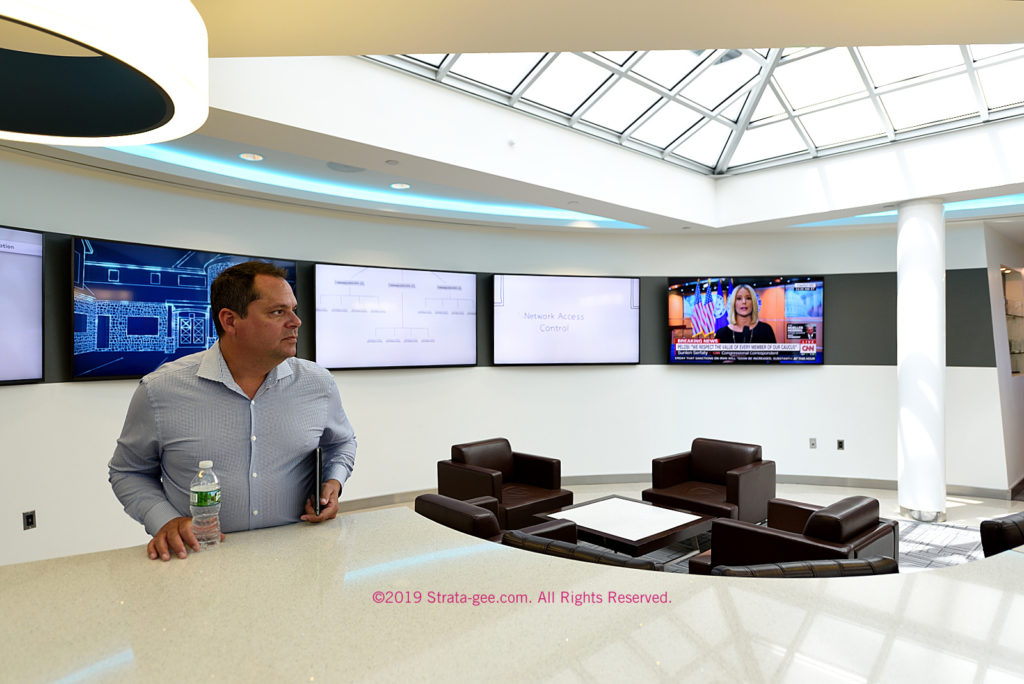
While I waited for John Clancy to join me from his office, I perused their experience center. If you haven’t seen it, it is pretty spectacular and I will be covering it later in this series. As seen above, John arrived to greet me and to give me an overview presentation of their latest Crestron OS3.0 software (which is very impressive and a big step for Crestron).
Work Home of Around 500 Engineers
We immediately drove to the Research Center. This is an impressively large facility (the picture doesn’t accurately convey the scale of this place…it’s huge! It is home to between 400-500 engineers. Let that sink in for a moment…how many manufacturers do you know that employ 500 full time engineers? Not many…
Approximately 400-500 engineers in the research center is an impressive number for sure. But this is not all of their engineers – they have other engineering departments stationed in other buildings around the campus. In this facility, most of the engineers are working on hardware projects, quality assurance (QA) testing, bulk development, and cloud development.
After check-in at the reception desk, we were met by Doug Jacobson, who is Crestron’s Director of Residential Technology. Doug was to be our tour guide for this portion of the day and he quickly launched us into the tour.
>>Click to see a slide show of all of my photos from Crestron’s Research Center<<
Cubicle City
After leaving the reception area, we went to a very large space that was filled as far as the eye could see with cubicles of the type you find in many “open” office floor space designs. It was interesting to note that they ran a low overall light level, with task lighting on each desk in each cubicle. Here were many of their engineers, although the first cubicle we came to was for Howie Balch, one of several of Crestron’s industrial designers.

I chatted with Balch for a few minutes, mostly discussing how they are using high-powered computer generated designs these days. While Howie remembers the good old days of pen on paper, he believes today’s computer-generated conceptual drawings give a better perspective on the scale, design, and potential feel of the product.
The Process of Product Development at Crestron
As we walked around, Jacobson chatted about the process that Crestron goes through in product development. In a nutshell, their team constantly scans the market, develops concepts they feel would drive the market, then engages various partners (like their dealers) to gauge their thoughts on these new concepts. In special cases, they go to consumers or enterprise end users.
This would be a good time to mention that Crestron is a huge, multi-billion dollar company whose biggest business is on the commercial and enterprise side. While a lot of technologies and products are relevant in both markets…many aren’t. Hence, the need for 500 engineers. This is an incredibly muscular engineering resource that outstrips that of most of their competitors.
PC Boards Displayed on Cubicle Walls
Also, I was pleased when Jacobson mentioned to me that the Crestron Home platform has a dedicated team (as does their Enterprise platform). Engineers rarely jump between the businesses, although in special situations that can happen.

While we strolled through the engineering level, I was struck by the number of printed circuit (PC) boards, some even active, that I saw hanging on the outside of a lot of these cubicles. In one case, a lighting control board was being tested right in the engineering offices – on their actual office lighting!

Proud of Their Accomplishments
Crestron designs, prototypes, and builds their own PC boards, and many examples of these were proudly displayed. By the way, most of their competitors rely on outside resources for this capability.

I love to see engineers who are proud of their work and aren’t afraid to show it off. They don’t often get this recognition from the market, so they celebrate it internally.

Operations Actually Use Their Own Innovations
As we continued to tour the facility we walked by a set of meeting rooms. Doug Jacobson wanted me to assure all my readers that Crestron is an avid user of their own creations…in this case, their meeting room scheduling system. It is simple to set, and very easy to understand (green means available, red means not available). With a couple of button pushes, we scheduled a walk up meeting.

A Heavy Investment in Prototyping Capability
We then walked onto a larger floor. This turned out to be their metal fabricating shop which is used for prototype creation. Crestron believes in quick prototyping – finding out fast if a design is going to work…or is a waste of time. The company has invested heavily in industrial-grade equipment to assist them in this process.

Machines such as a heavy-duty metal bending and cutting machines, an incredibly powerful FLOW water cutting machine, various other saws, drills, and more. Their machine shop has the capability to quickly make a one-off prototype that looks almost like a perfect replica of the final product. Again, for many manufacturers, this type of work is farmed out to outside shops – adding time and cost to the process.

Large 3D Printing Department Accelerates Prototyping
From here we moved to their 3D printing area – a technology that has totally revolutionized prototyping. Crestron is working on hundreds if not thousands of new products every year, so this part of their research center is almost always in use. Crestron’s prototyping shop has three large 3D printers that handle different sizes of output and types of material.

Of the three machines, the one seen above is the mac-daddy of them all – capable of creating the largest objects. Jacobson tells me that, depending on the size and the complexity of the prototype, they sometimes start the printer and let it run overnight – getting their finished prototype in the morning. [You can see the other two 3D printers in the slide show accompanying this post.]

>>Click to see a slide show of all of my photos from Crestron’s Research Center<<
What Crestron Did Not Want You to See
Now I’m going to show you a few images that Crestron did NOT want me to show you. But I’m going to show them to you anyway, because it is a true representation of what I saw while I was there. The reason Crestron did not want you to see these images is because they are concerned you will find them messy and, therefore, might think less of them.

But you should not think any less of them. I have been in engineering labs literally all over the world, and these images are representative of what I almost always find. You see, in these facilities, configurations are being tested and changed all the time. So temporary jigs are set up, cables are strung haphazardly, devices are pulled out and changed out for others of a different size and shape. In short, this is normal. If this lab was tidy and spotless – then I would be suspicious that I was being set up…being shown a staged crime scene.

Blown Away by The Amount of Testing Going On
When I left the Crestron Research Center, I was blown away by the amount of testing going on. In just about every corner, everywhere I turned, I saw various systems and configurations being tested. It was kind of mind boggling. When I mentioned this to Jacobson he said, “We don’t just recommend systems based on their specs – we actually test them. In addition, we test large system configurations thoroughly before installation to ensure solid performance.”
The company is serious about testing…but not just their products. All around I found lighting fixtures, motors and more from other companies. All are tested for compatibility and effective control by Crestron products.

100 Engineers Dedicated to QA Testing
Jacobson tells me that even Crestron authorized dealers can send, say a lighting fixture from another brand they need to install in a project, to be tested with Crestron dimmers. They’ll get a full report on its results, giving the dealer peace of mind that it can be used in a Crestron system. But one thing the dealer won’t get – a bill for this service…it’s free!

Remarkably, Crestron has at least 100 engineers dedicated to QA (quality assurance) testing… Obviously the company takes the quality of its products very seriously. So everything they make undergoes extreme testing, both in lab environments, and in real world usage testing.

With a line as diverse as Crestron’s, it is a heavy responsibility to conduct this much testing, but necessary when you want to be the leader in high performance, high-quality integration products. Of course, with the company serving both residential and commercial/enterprise markets, the complexity is compounded. For example, I saw a large enterprise cloud solution being tested. This required a string of sophisticated test routines pushing the configuration to the edges of its capability.
Engineers are ‘Advocates for the Customer’
All of this is done in what Crestron calls their QE Lab. QE, or Quality Engineer, is a more modern concept to what I tend to refer to QA or Quality Assurance. Jacobson told me that the company develops “test plans” for every product in parallel with the initial development of that product.
“QE reviews [testing] requirements right from the beginning,” Jacobson explained. “As original product specs are being created, QE is creating test plans.”
Doug Jacobson, Director of Residential Technology for Crestron
And tests plans are designed to test “to scale.” John Clancy noted that as Crestron Home OS3 was being created, it was tested to control 300 light loads in a massive test to scale in the Research Center. In reality, it is unlikely that many users of OS3 will need it to operate at that level, but it is part of Crestron’s testing strategy.
>>Click to see a slide show of all of my photos from Crestron’s Research Center<<
“Test plans include ‘corner cases’ – things most people wouldn’t ever try to do,” Jacobson noted. He added that QE engineers “are really the advocate for the customers.”

In fact, I had one engineer show me a binder of designated routines he was conducting on a system he was testing. It was a big binder with a lot of defined tests – and he was patiently going through them one-by-one, carefully logging his results.
A Torture Chamber of Horrors
In another section of the building, I got to see an extremely high tech environmental testing chamber where they conduct highly accelerated life testing. This is, in essence, a torture chamber of horrors for electronics, with the ability to subject the equipment to extremes of high temperatures, extremes of low temperatures, vibration, and voltage swings.

Tests are conducted by computer control and the temperatures can be adjusted slowly or rapidly from a range of -60°C -to- 100°C which equates to -76°F -to- 212°F. The base where products are placed is literally hammered from underneath to create vibrations ranging from 5Hz to 5,000Hz. Multiple items can be placed in the chamber (anchored down to the tabletop) and operations can be performed individually or on the entire group.
Let’s Talk About Extremes
I was told that the engineers keep pushing the extremes until the product fails. Not all products fail – about 75% don’t make it through. From the failure, engineers learn what components to replace in order to improve the unit’s ability to survive….in the extreme.

From here, Jacobson showed me a few examples of the extremes the company goes to in testing large-scale systems – with many tests in progress during my tour of the facility. The first one I saw was a video distribution system that was being tested for an impending large commercial installation (see photo above). During my visit, I must have seen several hundred flat panel screens in various tests in progress that day!
24-Zone Distributed Audio System Test

I walked by a rack with 24 iPods and asked Jacobson about what I was seeing. It was a 24-zone distributed audio solution being tested by having the iPods operate as a source for each zone and continuously playing music. It seemed just about everywhere I looked, there was some type of test going on.
Of course, if you are going to test a large scale system, you have to include all elements of this system. This includes motorized shades, light dimmers, touchpanels, speakers, remote controls, thermostats…even wireless door locks! As I contemplated the extent of many of the sophisticated installations that Crestron is involved with, I began to realize the challenge of truly testing a system so the company can stand behind it with confidence.
>>Click to see a slide show of all of my photos from Crestron’s Research Center<<
You’ve Got to Test Everything in the System

By the way, here’s a fun fact – if you look at the touchscreens in some of these photos, you’ll see a picture of a building. That is the actual building for the project where the system being tested will be finally installed.

A Bonehead Sensor, Perhaps?
Aside from the building on the touchscreens, you may also notice in the photo above some hanging pieces of paper. “What’s this for?” I asked as I physically lifted the paper. Instantly, I heard a relay click. Oh-oh!…What just happened?
Yes, your bonehead author of this post actually thought those hanging sheets was an attempt to hide something from me, so I lifted one! But I had inadvertently inserted myself into their testing routine, because those papers were covering occupancy sensors! Perhaps they are bonehead sensors…because they found one!

In my defense…lame as it may be…I am used to seeing things covered up in most engineering labs when I visit. That is due to the fact that many of these labs have secret projects or new products that they prefer not to have exposed at the time of my visit. Still…I should have asked before I lifted the veil!
An Obvious and Unusually Deep Commitment to Quality
One thing I can say that I’ve concluded from my visit to the Crestron Research Center is that this is a company that has made an above-and-beyond, deep commitment to product quality. The company has invested untold millions – if not tens of millions – of dollars into test gear and assorted machinery. I viewed desk after desk stuffed chocka-block with tens of thousands of dollars of test gear for that one bench. And with approximately 500 engineers – there’s a lot of benches.

I pushed Clancy and Jacobson on whether the company had gone overboard – perhaps over-investing, wasting money on machinery and processes that were readily available from outside agencies. To sum up their answer…maybe. But if you’re committed to creating, designing, prototyping, testing, manufacturing, (and testing again) the absolute best, most reliable products, as quickly, efficiently, and cost effectively as possible – they feel those investments are necessary.
This visit (including the totality of all the facilities I toured that day) was easily one of, if not the, most impressive visit to a manufacturer I’ve ever had. I’ll sum it up by saying it is hard to argue with Crestron’s success.
Coming Up…
I have two more installments coming from my visit to Crestron. The next installment is, in my mind at least, equally impressive – I’ll take you inside Crestron’s BRAND NEW factory in Orangeburg, NY. They call it the “Factory of the Future,” and based on what I saw…that is not hyperbole.
Learn more about Crestron at: www.crestron.com.
Leave a Reply