
This is Part 2 of Strata-gee’s series on my recent visit to Crestron. In some ways, as much fun as I had at their Research Center, I can almost say it was eclipsed (if only slightly) by a visit to, at that point, their yet-to-be-officially launched factory that was actually a couple of miles away from the main Crestron campus at a facility in the state of New York.
They call it their “Factory of the Future,” and after touring it…I can see why.
See Crestron’s brand new ‘factory of the future’…
I am not susceptible to motion sickness, but I almost felt as though I might be as John Clancy, Crestron’s VP of Residential, quickly drove me just a few short miles from Northern New Jersey to a new manufacturing plant in New York state. The area is very rural with lots of small two-lane winding roads cutting through forests with lots of dips and fast curves.
We were behind on our agenda and Clancy was moving quickly to the new facility to continue my tour. Then we came upon a small industrial park in Orangeburg, NY with a very large building featuring the Creston logo.
An Insanely Large Warehouse
A relatively new building, it was originally conceived as an insanely large and very modern warehouse. But when the company opened up a new warehouse facility in Texas, that took some pressure off this facility and allowed the company to divide it into two very large sections – one to remain a warehouse, the other to be built into a state-of-the-art factory.
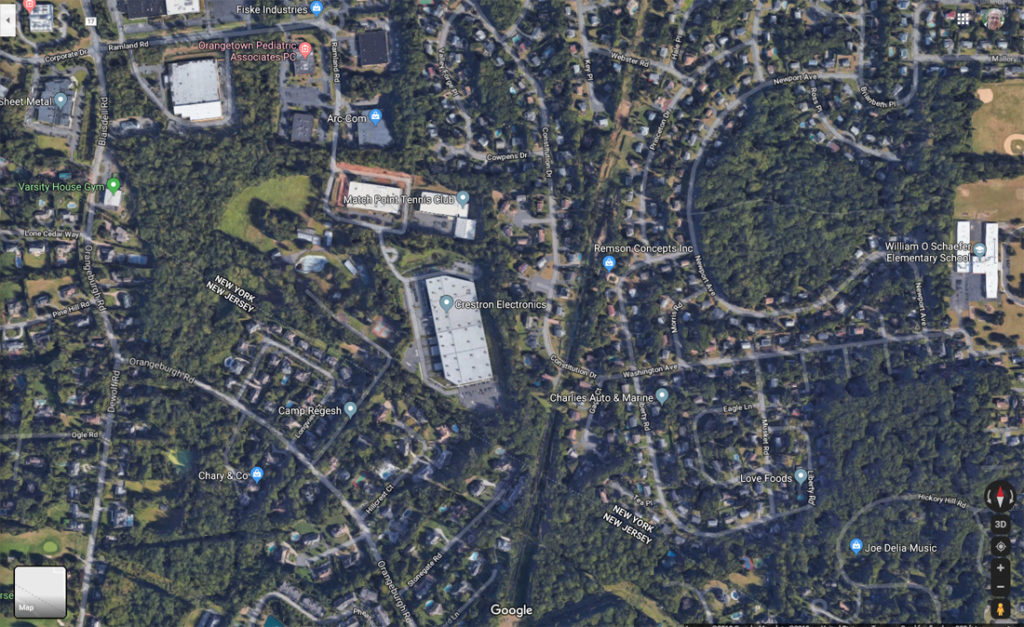
But Orangeburg turned out to be even more than even that. We were met at the entryway by Calvin Delano who is Crestron’s Director of Configured Production. Delano was to be our tour guide for this facility and he started by providing our entire group – we had been joined by Phil Thompson, Crestron’s Director of National Sales, who hadn’t yet seen this new factory – with special lab coats and protective glasses for our protection. Safety first at Crestron!
An Army of Service Techs Support the Line
Delano pointed out that all employees wear similar safety gear and even more, including special shoes that resist static electricity. (We had to stay within marked lines in the aisles so we didn’t inadvertently blow up any printed circuit [PC] boards!) Although our gear was not particularly stylish, it served its purpose well.

We started by entering their Service Department. It is a little hard to see in the photo above (be sure to click to enlarge it) – because it is HUGE and stretches all the way across the entire width of the facility – but Crestron maintains a very large, well organized, and complete repair facility that handles both their residential and commercial product repairs. The company has no fewer than 41 repair technicians who are ready to handle any problem with any model, no matter how complicated, in their technologically sophisticated line.
Product Reliability Testing Lab
Much to my surprise, adjacent to the Service Department is a Product Reliability Testing Lab where I got to see many more Crestron products going through a series of tests. I guess I had just assumed all of their testing took place in the Research Center. But this organization has some level of testing in practically every corner of their business.
For example, they have a vibration or “shaker” table – a pretty common test for most manufacturers who want to test to be sure product packaging is doing its job. But this particular testing machine is not your ordinary shaker table.

Over-achievers that Team Crestron are – they have a highly sophisticated, computer-controlled shaker table that runs various “road profiles” so you can take products on a virtual voyage of vociferous vibration. For example, you can simulate actual shipments…say from New York to Los Angeles starting on Interstate 80 across New Jersey and Pennsylvania with the actual level of vibration the product would actually face on this specific journey. Pretty amazing!

‘We Test to Destruction’
In another area, I watched the machine in the photo above running an automated routine with a vertical tower with a black cord connected to a beige box. The machine kept going up and down. At first, I couldn’t tell just exactly what was being tested.
Then Delano, perhaps seeing my puzzled expression, told me it was testing a retractable cable assembly that is used in some corporate conference tables. So this was a lifecycle test of the cable retractor itself. “We test to destruction,” Delano told me. This is the only way to know just how long these items will last – and can often generate a lot of product improvement ideas.

Tall, Transparent Phone Booths
Nearby was a series of tall glass enclosures – they kind of looked like tall, transparent phone booths. This time, I figured out pretty quickly that I was watching motorized blinds drive motors being tested for reliability. Yellow weighted bars just kept moving up and down at a pace dictated by the test’s computer control. There were different sized weights (compare the yellow bars on the left, to those in the next cabinet on the right) to test out the motor structures. It was kind of fun to watch…almost hypnotic! You know…like a lava lamp! (Do you even know what that is?)

Also in this lab were several environmental testing chambers, including one extremely large one you can see in the center-left of the photo below. If you look to the right, you see a few more smaller environmental testing chambers (beige colored) giving this lab the ability to do a lot of testing simultaneously. These chambers can test how well products (or parts or assemblies) handle temperatures from a low of an extremely cold -110°F to a high of a brutally hot +401°F.
Quality Assurance Lab

We then moved by a Quality Assurance Lab, further evidence of the company’s total commitment to testing. It was here where we came upon a large fully glassed in room. In the center of that room was a large machine called the Altera 10.10.8. Intrigued, I inquired as to what that machine is tests.
The Altera comes from a division of Nikon, and it is a highly precise, three-dimensional, coordinates measuring machine. Fully computer-controlled, the Altera uses precise sensors to measure a part to a microscopic degree – far more accurate than an engineer with a micrometer. All incoming parts, no matter their source (even from other Crestron divisions), are tested for ultimate specification accuracy.

A Warehouse Floor You Could Eat Off Of
We then moved into the warehouse section of the building. I don’t know if you’ve noticed throughout these photos, but this facility is amazingly clean. You could even eat off the floor in the warehouse!

Crestron’s warehouse uses closely spaced, tall racks, for very high capacity storage capability. This design requires a special forklift system that is just wide enough to fit down the rows, but can extend the full height of the racks. This design is not exclusive to Crestron, but it was interesting to watch this system in action during my visit. Seems quite efficient, and this warehouse ships the entire eastern half of the country. It also provides for pickup by local integrators.

Entering the Factory, It’s Immense
We then walked through a large, high-speed overhead door that separates the factory from the warehouse/service/testing area. The minute you walk through that door, the immensity of the space hits you.

It is hard to truly appreciate just how large this space is from the photos, but this is a 90,000 sq. ft. manufacturing facility. There are 16 departments arranged for the purpose of manufacturing some of the most technologically sophisticated products in a facility that has been designed from the ground up for speed and efficiency.

The Battle to Eliminate ESD
Again, I was struck by the cleanliness of this facility. It is immaculate. Floors were spotless, which I suppose is necessary in a facility that is designed to provide an end-to-end manufacturing environment fully protected against electrostatic discharge (ESD).
The first area we came to was called the Custom Enterprise Staging Area. Here, the factory stages products built for large enterprise projects for an additional step in the process – provisioning.
A Station for Provisioning
Based on the specific project specifications, the factory provides full Digital Media configuration so that when the items arrive at the job site, they can be pulled out of the box and popped right into the rack ready-to-go. A computer controlled process, each stack of products travels through the process with documentation verifying the necessary configuration information.

We carefully stayed within the marked lines on the floor to avoid any static accidents, as we were not completely protected in this regard. Coming upon an area of strange looking racks, I discovered that Crestron uses custom designed parts racks which protect parts from ESD. An added, but necessary detail – especially when working with raw electronic components that are sensitive to – and can literally be destroyed by – ESD.

State-of-the-Art Surface Mount Machines
Next Delano showed me a large station with multiple surface mount machines. What’s a surface mount machine, you ask? A blank pc board enters the machine and then a robotic armature rapidly inserts all of the components that are needed for the circuit. This means resistors, capacitors, chokes and coils, integrated circuits, etc. – which are all needed to make the product work – are very rapidly inserted into the pc board.
If you’ve never seen one of these machines in action, you’re missing a real treat. Surface mount technology allows these computer-controlled automated machines to add or mount the individual electronic components on a printed circuit board at an insanely fast pace – so fast you can’t even actually see them being inserted…you just see the circuit magically begin to appear. It’s amazing.

Blazingly Fast and Accurate
The basic technology has been around for many years, but Crestron is using the absolute latest generation of Panasonic SMT machines that are truly state-of-the-art…and are blazingly fast and accurate. Those tapes you see hanging down on the front of the machine are kind of like ticker tapes that hold the components and feed them to the armature when needed. All a human needs to do is to keep feeding more tapes of components as they run out.

In the photo above, we are further down the manufacturing line and an employee is visually inspecting a board through a high-power magnifying glass make sure there are no defects. As you might suspect, Creston manufacturing does multiple tests of every product. You’ll see more examples of that below.
High-Speed Testing via a ‘Flying Probe’
Continuing to move down the line, this device shown in the photo below is a test machine called the SPEA Flying Probe Tester. To understand what this does, imagine an engineer sitting at the end of the production line with a probe connected to a meter to test each circuit board coming off the line to see if it is operating correctly. He touches a point, takes a measurement, looks at the meter to confirm that it is performing to spec. Now he touches the next point to be tested – on a pc board there can be thousands of points to be tested. This is going to take a long time!

However, imagine if your engineer was computer-controlled, fully automated, and able to conduct 180 such tests a second! Enter the SPEA flying probe tester. It’s called a flying probe because its automated test routine CAN conduct up to 180 such tests every second – that probe is truly flying! Want to see this in action? See a video from the manufacturer below…it’s pretty amazing!
Our PC Boards are Complete, On to Assembly!
So here we are at the end of the line! Our boards have been fully stuffed, soldered, checked, and then tested. They are perfect and ready to go to the next stage of manufacturing – assembly into their respective product.

As I admired the finished pc boards, I noticed a large area off my right that looked like cubicles. I asked Delano what this area was for? Who are these people. “That’s our production engineering team,” Delano told me. It is not common to see the production engineers right on the factory floor…they are typically in an associated office building, more remote from where the action is.

Recently, I mentioned this in connection with my tour of James Loudspeaker. Perhaps this is becoming a new trend! But even Delano noted its rarity, as well as how it has really helped to promote team work between these engineers and the folks working on the factory floor.
An Amazing 24 Product Assembly Lines
Now, we have arrived at the assembly lines. This new factory for Crestron has 24 such top-level assembly lines continuously in action to build products to fill dealer orders. By the way, 24 assembly lines is a lot! While there, I noticed the gentle whir of activity as the facility was in full swing, even though it had not been officially announced at the time of my visit.

This facility was noticeably quieter than others I’ve visited, yet there was definitely a blur of activity as multiple lines were in full swing. Clean, well-lighted, quietly efficient, fully active…this new facility is definitely one that Crestron can be proud of.

The Efficient Movement of Parts for Assembly
Racks of sub-components waiting for their role in final assembly were spread all around the production lines, helping demonstrate the efficient flow of items needed for assembly. I also saw testing…lots and lots of testing…taking place within various lines.

In fact, I saw so much testing going on of boards, sub-assemblies, assemblies, finished goods…I asked Delano how many tests each product goes through in the manufacturing process. His answer? Every single product they manufacture goes through somewhere between 12 to as many as 30 separate checks! Every one…
Open those boxes of Crestron products with confidence!
Leave a Reply