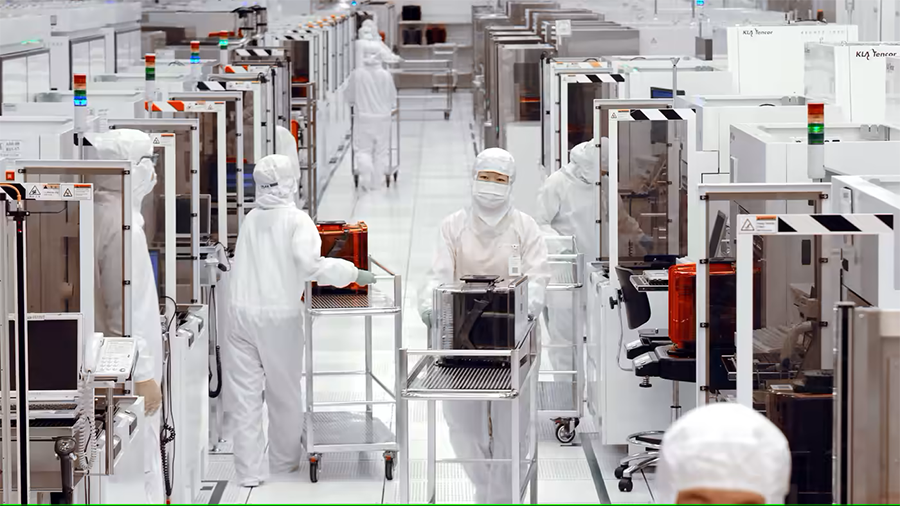
Ever since supply chain shortages hit many industries, particularly in relation to the availability of integrated circuits or chips, there has been a massive scramble to increase capacity and to build new chip fabricating facilities (fabs) or factories. There has been a series of announcements from huge companies like Intel, Taiwan Semiconductor Manufacturing Co. (TSMC), Samsung, and others launching massive multi-billion projects to add more chip production facilities.
There’s just one problem…the equipment they need to build these facilities are themselves delayed.
See more on the supply chain shortages delaying new factories to help the supply chain
The plan went something like this – the first step to try and address the chip shortage was to add production lines within existing facilities that had space for expansion. The second step was to launch massive projects to build more production facilities around the country…and around the world.
New Chip Fabs Take 3 Years to Construct
Building an all-new facility from the ground up typically takes three years to accomplish. However, in the step one scenario above, some time can be saved by utilizing available space in existing facilities and adding new production lines.
With chip demand still at all-time highs, nothing could be more important than building additional production capability so that more chips can be manufactured. Massive industries like electronics and automobiles have seen their revenues crushed and operations thrown into disarray as products were delayed – or even canceled – as a result of the chip shortage.
A Hall of Mirrors
But now the Nikkei is reporting that a new problem is delaying all projects, including the faster, easier option of expanding lines in an existing fab. And the reason for this new delay feels like we’re trying to find our way through a hall of mirrors.
The reason, says this latest report, is that “Leading chip tool makers…are warning clients [the Intels, TSMCs, & Samsungs of the world] they will have to wait up to 18-months for some crucial machines” that are necessary for their projects. Makers of the machinery that fabricates chips are reporting supply chain-related shortages “in everything from lenses, valves and pumps to microcontrollers, engineering plastics and electronic modules.”
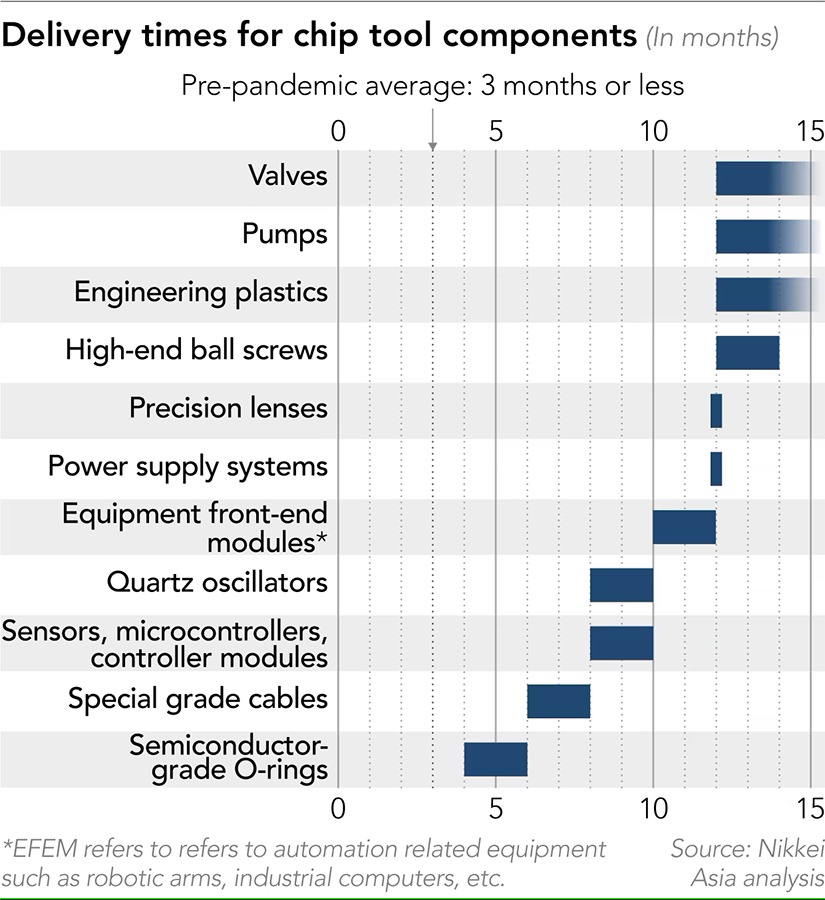
With Demand for Chips Up, Demand for Chipmaking Equipment is Up As Well
And like an echo of the overall market, as this supply of critical parts is drying up, demand for chipmaking equipment is “surging,” the Nikkei says. Yep, just like we all experienced with toilet paper in the Spring of 2020.
So how are key semiconductor manufacturers reacting to the news of parts shortages? They are panicking. According to the report, TSMC, United Microelectronics Corp. (UMC), Intel, and Samsung each have plants scheduled to come online soon, perhaps as early as late next year (2023). So many of them are deploying their top executives to visit the headquarters of various top machinery and parts makers like Applied Materials, KLA, Lam Research and ASML in order to explain (i.e. pressure, or perhaps, beg) them to deliver the goods in time.
Begging a supplier to deliver goods ordered in the face of supply chain shortages is probably a familiar predicament for many Strata-gee readers.
Average Delay is 18-Months, Delay of Individual Components Can Be Much Longer
And while the overall average is a delay of around 18-months, the wait for certain individual components can be even longer. Pre-COVID delivery times could be as quick as around 3-4 months, according to this report. Last year (2021), those delays stretched to 10-12 months.
What about now? Chip manufacturers say the delays are the worst they’ve seen in decades. For example, testing gear from KLA (a U.S. company) has a current wait time of “more than 20 months.” Equipment used in making substrates – material that carries chips prior to being mounted in PC boards – is experiencing wait times “up to 30 months.”
Does Misery Truly Love Company?
Does misery love company? The chip manufacturing gear suppliers say they are the victims of the same supply chain issues that are impacting their customers – the chip manufacturers. They have no choice but to pass along the delays they are being hit with as they attempt to acquire the components necessary to make their machinery.
I’m feeling numb hearing this prolonged [component] lead time. I’m squeezed between our chipmaking clients and my component suppliers, and it’s really painful”
U.S. chip manufacturing equipment maker
TSMC told the Nikkei that they are already falling behind in their originally planned and announced fab project schedules. They have several projects planned for new chip fabs in the U.S., Taiwan, and Japan. First up was supposed to be the U.S. facility, but it is behind schedule due to supply chain issues AND labor shortages.
The Component Shortage Situation ‘Is Still Deteriorating’
Samsung declined to comment on the Nikkei report. UMC, the fourth largest contract chipmaker in the world, confirmed to Nikkei that they have deployed a variety of its top management to meet with component suppliers around the world, but has only learned that “it will not be easy to move up its schedule.” In fact, they say suppliers told them that the component shortage situation “is still deteriorating” and there is no opportunity for improvement earlier than the second half of 2022.
Perhaps most concerning is that ASML says that “there is a consensus in the industry that the chip shortage could last [another] two years. The entire industry is ramping up to address this.”
There are so many bottlenecks, from different components to logistics, and they just cropped up one after another. It’s like deja vu. The unprecedented supply chain crunch that happened to automakers, PC makers and smartphone makers is now hitting global chipmakers.
Top manager at U.S. chip equipment manufacturer
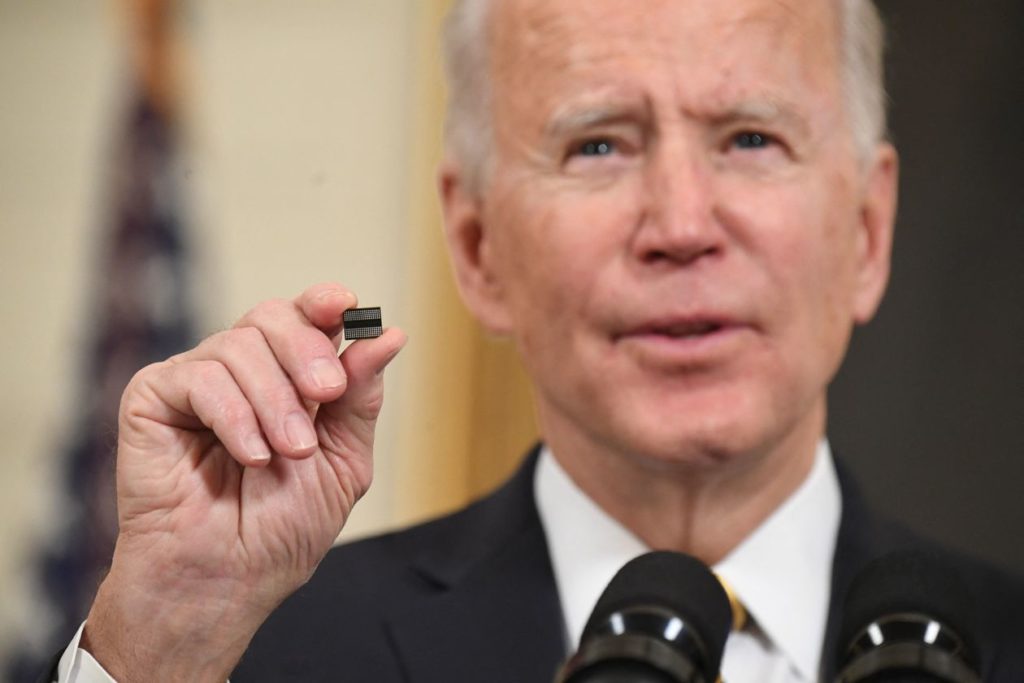
Is It a Bubble? ‘Signs of Slowing [Demand] for Consumer Electronics’
Complicating matters is the fact that some of the parts and component suppliers are reluctant to boost their production. While there is an unprecedented level of demand, some feel it is a bubble that will soon burst. If they build up too much capacity and then the bubble does burst, they could be left holding the (very expensive) bag as demand falls.
This is not as crazy as you might think it sounds. Some in the investment community see the possibility of a bubble burst as a real risk that manufacturers have to consider. Gokul Hariharan, a JP Morgan analyst covering the technology, media and telecom segments told the Nikkei that these suppliers must take slowing demand into consideration.
From an overall semiconductor industry perspective, my biggest concern is still whether demand growth is sustainable. We already see signs of slowing [demand] for consumer electronics, and that could eventually have some implications for the semiconductor supply chain. I would say the variables are still going to be more about demand. The magnitude of the cycle will depend upon how much [chipmaking] supply comes online.
Gokul Hariharan, JP Morgan technology, media, and telecom analyst
A Heightened Risk of Recession
There are so many complicating factors right now, including raging inflation, the Russian invasion of Ukraine, interest rate increases by the Fed, global supply chain disruptions, and deteriorating consumer confidence. Many economists believe that we are seeing increased risk of a recession.
And with a recession, you normally see a collapse in demand for goods. For many people, planning their business for one year is tough. Imagine you are a semiconductor manufacturer deciding whether to build a new fab that will take three years before it comes online, and even longer before it reaches full capacity.
Can you confidently predict what the world will look like three years from now? Yeah, me neither…
[…] Read More: https://www.strata-gee.com/whats-delaying-new-chip-fabs-to-reinforce-the-supply-chain-yep-the-supply… […]